In 2015, a monkey incident took place and the approval of the Shadgan steel project as one of the provincial steel projects was a promise of sustainable employment in the region.
In 1387, the implementation of the plan of Shadgan Steel Company was started, but due to the lack of liquidity of the government, this plan did not go well until in 1393, 65% of the shares of Shadgan Steel were transferred to Khuzestan Steel.
Following the implementation of this project, a land area of 256 hectares in 2 phases was examined in the deprived area of Shadgan, 35 km southeast of this city, and after that the construction project flourished and progressed rapidly until in 2016, an iron production unit was established. The sponge was used.
Let’s get to know Shadgan steel industry
Foreword
Iron, this precious mineral, was a hidden treasure of God. This lasting deposit came out of the soil one day by the mighty hand of mankind and was placed in the places of cities and places of human life with a dazzling brilliance.
From the distant past to the present day, iron and steel have marked a brilliant era in the ups and downs history of human civilization.
Historical researchers know the influential era of metal as the “Iron Age”. Although the secret of how the first molten particles were separated from the stone and turned into tools to be used by man has not been fully revealed to any researcher, but the ancient Scholars believe that perhaps, ancient people have accidentally witnessed this important thing in the warm presence of “fire” and “stone”. Since then, humans have used this discovery as a gift from God in the historical evolution of their means of life and effort.
Yes, this is God’s tradition, the sights should be learned, the experiences should be accumulated, the accumulated should become knowledge, and patience along with effort should come to the aid of knowledge and little by little the evolution of knowledge and human civilization would be formed.
In this way, iron and fire became inseparable companions and tools of civilizations. Until today, these two, one cold and firm and the other rebellious and restless, have always accompanied and helped human explorers in the path of evolution and development.
But in the meantime, the ancient land of Iran and the green plains of Khuzestan are among the proven and recorded origins for the development of human knowledge in the Iron Age.
A group of archaeologists consider the early inhabitants of the current land of Iran to be the first smelters of metals in the world.
Iranians living in the Khuzestan plain, as they were leaders in urbanization, agriculture and irrigation of their time, have been border guards with culture and brave defenders for Iran, this cradle of culture and civilization.
Emergence of steel industry in Shadagan
Shadgan, with the traditional name of “Falahieh”, is a well-known name among the natural habitats of Khuzestan province due to the fame of its beautiful wetlands.
This well-known region and its warm-hearted and hard-working people are now on the threshold of a new experience in the field of the country’s steel infrastructure industry, relying on the hard work and enthusiasm of its youth.
As evidence of the great progress achieved in recent years with the establishment of the “first Iranian direct recycling factory” in the heart of this land, the movement towards a bright future has begun in the Shadgan steel industry.
“Shadgan Steel Industry Company” is now a famous and familiar name in the specialized field of steel in the country.
Since 2002, this company has been investigated with special attention to the development needs and environmental considerations of the region.
The executive operation of the 256-hectare project was started in 2015 with the overall goal of developing steel in Khuzestan province, creating jobs and removing deprivation.
The huge project of Shadgan Steel includes the direct regeneration and steelmaking sectors. The executive operations of the factory in the direct reclamation section began seriously in 2013 and the project was followed by using the technical engineering facilities, experience and management of Khuzestan Steel Company.
Less than three years later, in 2016, after going through the trial stages and producing the first shipments of sponge iron, this important and influential regional national project was officially opened with the presence of officials, citizens and hardworking employees of Shadgan Steel. The final capacity of Shadgan Steel’s direct recovery department is 800 thousand tons and the steel making department is expected to be 1 million tons, which can be expanded up to 2 million tons.
The first in Iran and the world
An important point that is the lasting pride of every Iranian, especially the employees, engineers and those involved in the Shadgan Steel project, is that the direct regeneration section of Shadgan Steel is actually the first factory in the world that is based on a completely Iranian technology and method called Persian Reduction, or in short, “Pard” is made.
Previously, the design of steelmaking processes in our beloved country of Iran was based on global technologies, including Midrex. But the need to get rid of dependency on the one hand and the need to update on the other hand prompted the internal experts of steel to think of a new solution.
Therefore, in recent years, Iranian experts have spent a lot of effort in this field. The sacred efforts that were followed with the aim of consolidating scientific independence through the localization of steel technology and finally gave results during four decades after the Islamic Revolution.
For the first time, Iranian research engineers succeeded in using direct regeneration technology and built a factory whose product is sponge iron produced in an entirely Iranian way, equal to global quality. This new method, in the name of our dear country, Islamic Republic of Iran, has been registered globally in Europe.
The direct regeneration of Pard has been used in the construction of three steel complexes in the country, namely Shadgan, Niriz and Miane steels. In the meantime, Shadgan Steel Co.’s Ahyam Direct Factory has been a pioneer, and while proving the success of the Iranian Fard system, it is also considered the first unit opened based on this technology in the world.
Direct resuscitation department
Direct recovery of iron ores and electric induction furnaces is one of the conventional methods of steelmaking in countries that have abundant natural gas resources. At the same time, due to the possibility of pollution control and energy recovery, this method is more compatible with the environment.
In this method, in short, concentrated and ground iron ore is used as iron oxide pellets.
First, pellets or the main raw materials of the factory are supplied from internal sources and unloaded and accumulated in the material storage area. Pellets are gradually transferred from open warehouses to storage tanks by a conveyor belt system. Then, the same system, in the next step, directly enters the pellets from the highest area into the regeneration furnace.
The iron ore pellets in the furnace move along the path of the recovery zone. It is at this time that, while immersed in the regeneration gas and high heat, the main chemical reaction in the regeneration process begins, which penetrates from the surface to the center of the spherical mass of the pellet.
During this reaction, the reducing gases H2 and CO, which have a strong desire to absorb oxygen, combine with the oxygen in the iron particles and turn into H2O and CO2. The pellets, which have completely lost their oxygen during this chemical reaction, turn into iron with a high degree of purity.
As air or oxygen escapes from the pellets, small holes are left in the spherical body of the pellets. Therefore, henceforth, the name of sponge iron is applied to them. In the next step, while the sponge iron grains are still moving vertically from top to bottom inside the furnace, they reach the lower chamber of the furnace to be in contact with the gas. The coolant in this area will lower its temperature and leave the furnace with an ambient temperature.
In this process, hot and cold gases are used in a controlled process for the hot stage of regeneration as well as the cooling of the output product. So that the gas used in this section circulates continuously in the factory’s integrated and closed system. With this measure, while reusing heat energy, gas wastage is also prevented.
Sponge iron in the furnace has a strong tendency to re-react and recombine with oxygen. For this reason and in order to avoid environmental risks, by producing feedback gas and re-injecting it in the furnace wall as well as sponge storage tanks or product silos, the penetration of H2 and CO gases into the paths and product tanks is completely prevented.
The task of supplying electricity to this large factory is also entrusted to a special 33 kV substation, which is located in the ring of the country’s 400 kV network.
This huge power station is built on a land of 7.5 hectares located in the factory area.
Shadgan steel substation currently has six input feeders, which can be expanded to 22 feeders by starting new parts of the factory.
The sponge iron produced by the factory is currently being transferred to Khuzestan Steel Company for the steelmaking process.
In the near future, with God’s help and the efforts of the employees, the steelmaking department of the Shadgan Steel Industry Company, which has already started, will be completed, so that this important thing, that is, the melting and casting of billet ingots and the production of raw steel products, can also be done in Shadgan. accept
Steel sector
This section includes material handling units, electric arc furnace, crucible furnace, and steel casting machine.
With the construction and completion of the Shadgan steelmaking department, the entire process of steel production from iron ore pellets to billets, blooms and other products will be carried out in this factory.
According to the planned process of the production line in Shadgan Steelmaking, first, a suitable combination of sponge iron product with scrap iron is melted inside a 140 ton electric arc furnace. Then by injecting auxiliary materials such as coke, lime, dolomite and oxygen, molten steel is obtained.
Then, after separating the last impurities called slag, the molten steel is discharged into a special pot.
When the melt is placed in the furnace, it is time to find the desired analysis by adding materials such as ferro-silica, ferromanganese and silicon-manganese according to the customer’s request.
Shortly before the last stage, sampling and laboratory control, as well as the separation of other impurities, take place.
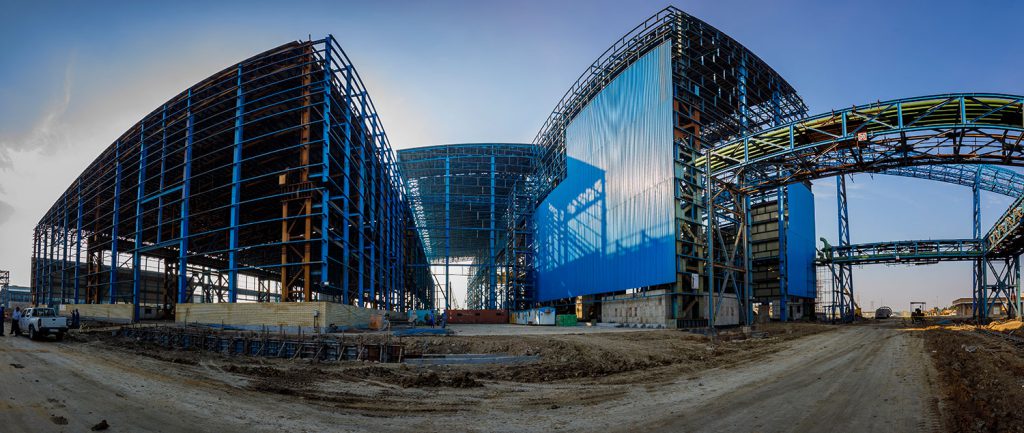
In the last stage, while the argon gas is blown from the bottom of the furnace into the melt and then the gas and electricity of the phases are cut off by the powerful steelmaking operators, the furnace is placed in the path of the overhead crane and enters the casting section.
Among the advantages of using the Patili furnace, we can point out the production of better quality melt, achieving the desired casting temperature, setting the ingot analysis according to the customer’s order, high work speed and increasing the temperature of the melts that have had an unwanted temperature drop.
The steelmaking department of Shadgan Fould includes a casting machine with six billet lines.
After the melt passes through the primary molds and the initial wall is formed, the ingots are formed and pushed forward in the molten state but close to solid.
Before the high temperature drop, the ingots are cut by gas nozzles in precise lengths according to the order and moved to the cooling bed.
The final product of Shadgan Steel ingots at the end of the production line in the steelmaking department is transferred to the ingot warehouse by another overhead crane to be sent to the company’s customers.
The establishment and development of Shadgan Steel Industry Company, which is the result of the efforts and specialized efforts of proud engineers and technicians of our country, is an important and long step in the production of an infrastructure and high-quality product in line with the increase of national production.
The happy citizens of Sharif Shadegan consider the emergence of this company as the blessings of the Islamic Revolution and the beginning of a great transformation in the elimination of deprivation and the all-round development of this talented region.